PLC (Programmable Logic Controller) and DCS (Distributed Control System) are both widely used in industrial automation, but they have some key differences:
PLC vs DCS:
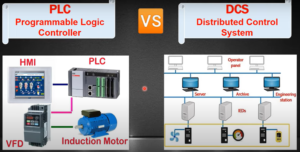
1. Architecture: PLCs are generally stand-alone controllers that are used for specific control tasks within a machine or process. DCS, on the other hand, is a networked system that connects various controllers spread throughout a plant or facility.
2. Scalability: DCS systems are typically more scalable, allowing for easier expansion and integration of new components or processes. PLCs can also be expanded but may require more manual configuration.
3. Control Philosophy: DCS tends to be more suited for complex processes that require coordination and communication between multiple control units. PLCs are better suited for simpler, standalone control tasks.
4. Programming: PLC programming is typically done using ladder logic or other programming languages specific to PLCs. DCS systems often use graphical programming environments that allow for easier configuration and visualization of the control system.
5. Maintenance and Support: DCS systems may require specialized training and support due to their complexity and networking capabilities. PLCs are generally simpler to maintain and troubleshoot.
Both PLC and DCS have their own strengths and are chosen based on the specific requirements of the application.
Not sure which to choose for your project? 📩 Contact us for expert advice.